
Basic Clamp Types and Application Scenarios
In the market, we can find many types of clamps, each with its specific application areas and advantages. The first is the stainless steel band clamp, which is suitable for high temperature and high pressure environments that have high requirements for durability and corrosion resistance; the second is the spring clamp, which is known for its simple and quick installation and is often used in automobile manufacturing and other industries; There are also some customized models for special purposes, such as rubber ring clamps with strong waterproof and sealing properties.
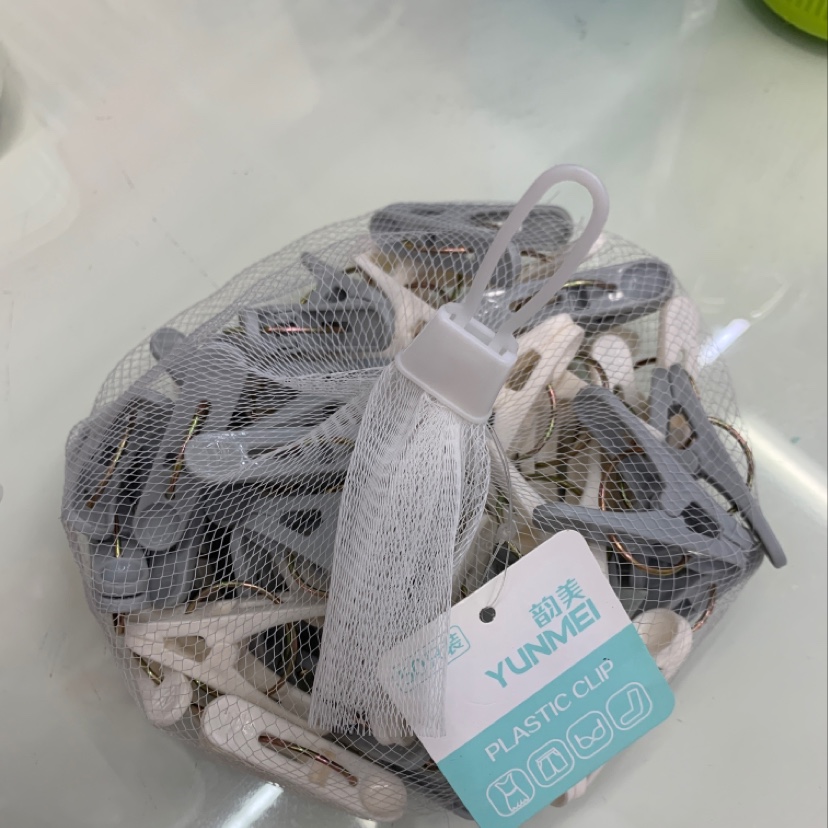
In order to help you better understand and choose products that suit your needs, we will show the application of various clamps in different environments through a series of actual construction photos. This allows you to not only visualize how they work, but also understand their strengths and weaknesses, so that you can determine the required category more quickly.
Material comparison: metal vs non-metal
When it comes to material selection, there are usually two main options to consider-metal (such as stainless steel, galvanized steel) and non-metal materials (such as plastic, nylon). Metal clamps have excellent mechanical strength and good durability, especially suitable for outdoor harsh conditions or the use of chemical industry; and non-metallic materials are favored because of light weight and not easy to rust, widely used in food processing and other fields.
However, it is worth noting that the price difference between the two materials is large, so you need to consider factors such as budget and personal preferences before making a decision. For example, some high-end brands of PVC coated stainless steel clamps can not only maintain the advantages of traditional steel but also overcome the problem of easy oxidation, which is one of the most cost-effective options.
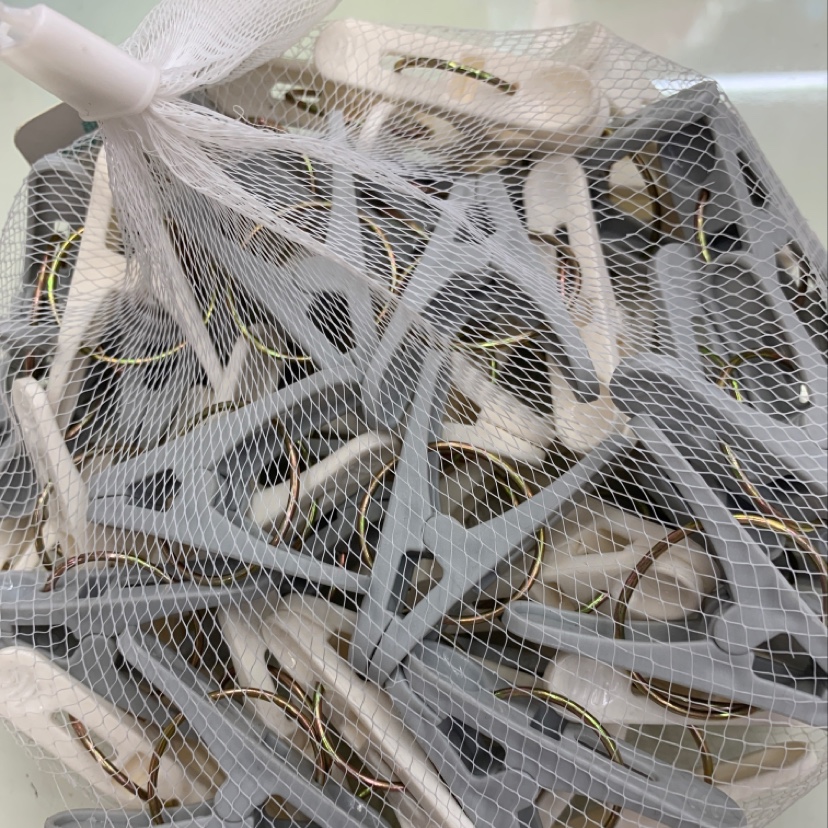
Importance of Dimensions
The correct selection of the appropriate size of the clamp is very important to ensure that the connection is stable. If you choose a product that is too large or too small, it may cause water leakage or other safety hazards. Therefore, we need to master a set of simple and easy methods to make accurate measurements:
- -Use a vernier caliper to accurately measure the outer diameter of the pipe;
- -Confirm whether the interface is flat and smooth without convex part affecting close contact;
- -Refer to the table provided by the manufacturer to select the appropriate specification.
In addition, we have prepared a detailed chart showing common problems and solutions to make it easier for readers to understand and avoid similar mistakes.
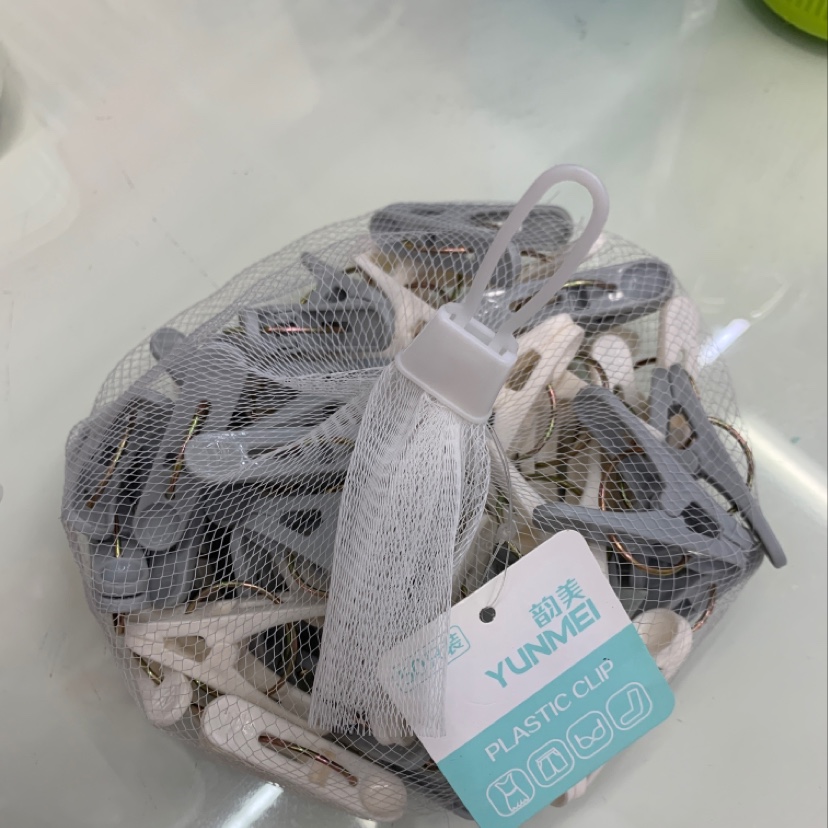