
Clamps play an integral role in modern engineering and manufacturing. Whether it is automobile maintenance, pipeline installation or mechanical equipment assembly, an efficient clamp is a key component to ensure the stable operation of the system. It can not only effectively fix the pipeline interface, but also withstand the test of various harsh environments such as high pressure and high temperature.
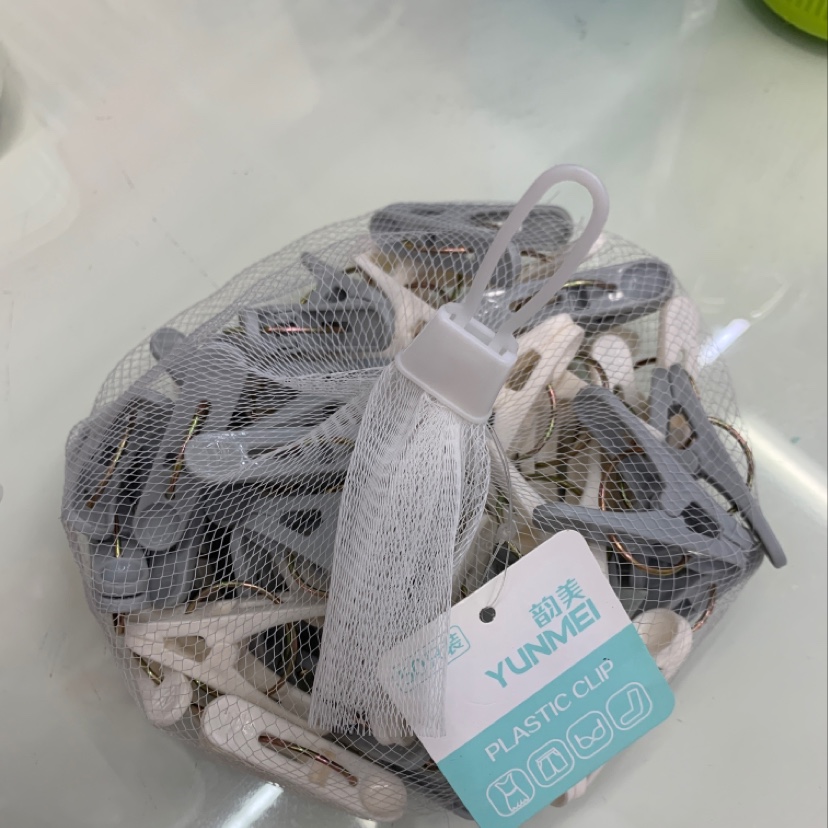
Through actual cases, we can see that in many large-scale projects, the correct use of appropriate clamps can not only greatly reduce the safety hazards caused by loosening or falling off, but also significantly reduce the cost of later maintenance. Therefore, it is very important to choose a high-performance and durable clamp.
The common clamp forms on the market mainly include screw type, bolt type and self-locking type. Each has its own unique features and technical parameters:
Spiral clamp: It has good elasticity and sealing, and is suitable for application scenarios that require quick disassembly and assembly;
Bolted clamp: Provide higher tensile strength, suitable for heavy equipment connection;
Self-locking clamp: The tension can be easily adjusted without tools, which is convenient and fast.
According to the needs of different projects, reasonable selection of the corresponding type of clamp can greatly improve work efficiency and extend the service life.
Stainless steel, carbon steel and other alloy metals are commonly used in the manufacture of clamps. These materials have different physical properties and corrosion resistance:
- stainless steel: acid and alkali corrosion resistance is superior, widely used in chemical and other industries.
- Carbon steel: Low cost but easy to rust, suitable for short-term use in general environment.
- New composite materials: In recent years, a high-strength plastic matrix reinforced fiber material has gradually emerged, which is not only lightweight, but also wear-resistant and not easy to age.
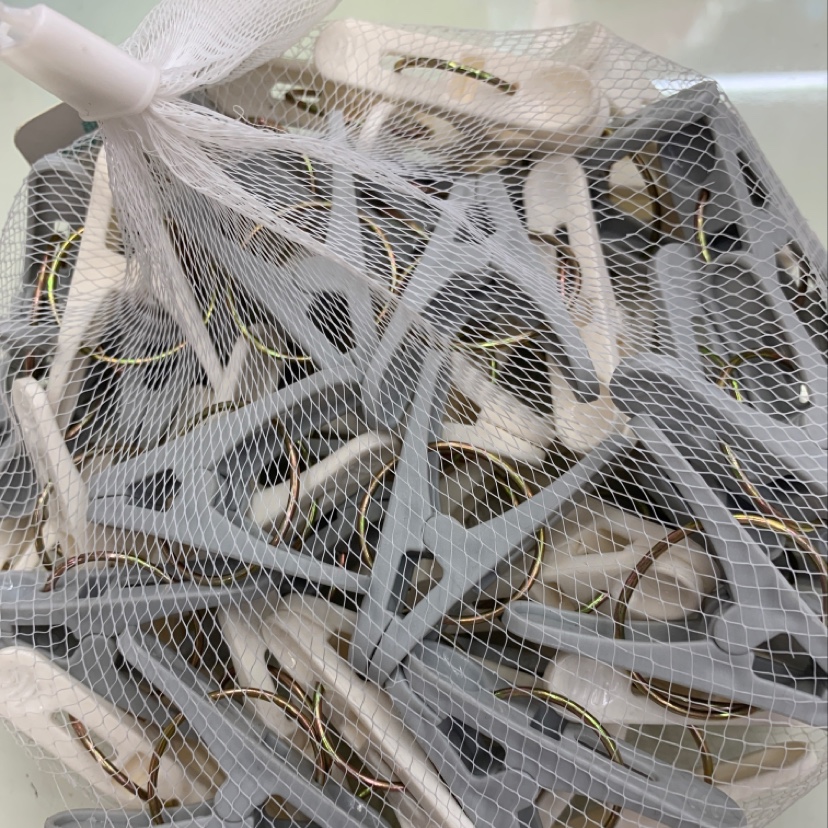
With the progress of science and technology, more and more new materials are being developed to improve the shortcomings of existing products, bringing more possibilities for the development of the industry.
high quality clamps are often reflected in many nuanced designs. Precise size control, fine surface treatment process and special anti-slip tooth pattern are important indicators to measure the quality of products. Excellent brands strive for excellence in every aspect to ensure that they maintain a lasting and stable clamping force even under the most demanding working conditions.
For example, some high-end models use laser cutting technology to achieve higher precision molding; some products are equipped with special coatings that can be unaffected by prolonged exposure to humid air. All this effort has only one purpose-to allow users to complete each task with confidence.
Understanding the relevant regulatory requirements for the production and sales of clamps at home and abroad is a part that cannot be ignored when purchasing. Brands certified by authoritative organizations usually have the following advantages:
-comply with strict national and regional safety regulations
-have a complete quality management system
-provide comprehensive technical support and service guarantee
Compliance production is not only the performance of corporate social responsibility, but also a prerequisite for effective protection of consumer rights. When selecting products, we should give priority to those who have achieved ISO or other internationally recognized certificates.
The valuable experience and insights from front-line engineers provide us with a wealth of reference materials. They described the various challenges they encountered in the field and their corresponding solutions. For example, in a complex oil exploration platform, due to the narrow space is difficult to display regular maintenance means, the use of a small hydraulic wrench with a remote control device with a specific specification of the self-locking clamp successfully solved the problem.
This kind of practical experience tells us that only by fully considering the changes in the actual situation can we formulate a more reasonable construction plan and maximize the advantages of each component.
In order to extend the service life of the clamp, we need to master some basic maintenance knowledge. Regular visual inspection, cleaning dirt debris is one of the very necessary steps. In addition, proper application of lubricating oil can help slow down the rate of friction and wear. It is worth noting to avoid the risk that excessive tightening or improper force may cause permanent deformation or even fracture.
If any abnormal situation is found, please be sure to follow the instructions to implement the corresponding repair measures, do not blindly repair yourself to avoid greater losses. Developing good operating habits is important for maintaining long-term reliability.
At present, the whole industry is moving in the direction of more environmental protection and energy saving. Many manufacturers have begun to try to recycle used parts to re-manufacture new products to reduce resource consumption. At the same time, we are actively exploring how to reduce energy consumption and develop low-carbon production processes. This transformation not only helps to reduce the pressure of environmental pollution, but also wins more market share and social reputation for enterprises.
We hope that in the future, more green ideas will run through all aspects of various fields, so as to jointly build a beautiful world in which human beings and nature coexist harmoniously.
Labs of well-known brands often carry out a series of simulation tests on their products under extreme conditions. These tests cover different temperature ranges from extreme cold to extreme heat,
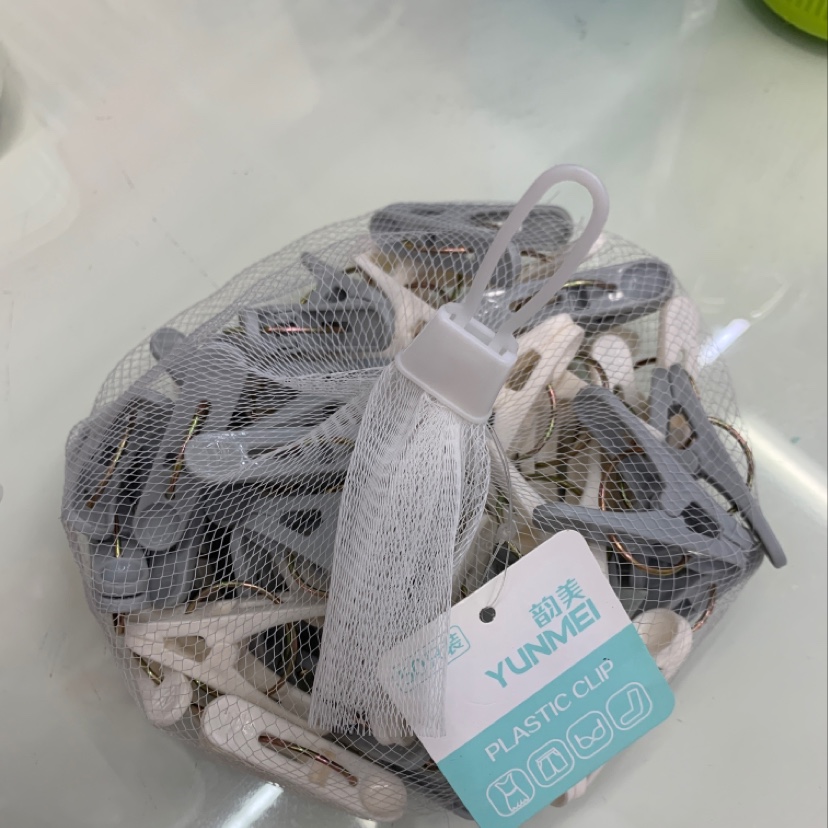